deformation sensing robot
2019 | expanding foam, charcoal, electronics
During my semester thesis at ETH, I developed a deformation sensing soft robot. Soft robots are a family of robots characterized through their soft, deformable body with elastic moduli similar to human tissue. They can be used in applications where traditional robots either cannot operate or could inflict damage or injuries to their surroundings or the operator. Such tasks can be found for example in the medical field, at inspection jobs in chaotic environments or as companions and entertainment for people.
A cheap and easy to work with material for the body of a soft robot is expanding PU (polyurethane) foam. It can be cast into molds produced in a 3D printer. Different methods of actuation for these robots have been developed, for example cable pulleys, pneumatic chambers, shape changing materials or combustion. In this work cable pulleys (”tendons”) were used as they are cheap and easy to produce, install and control. Due to their soft nature, inferring the pose of the robot is not straightforward, even if the input for all actuators is known.
A way to determine the actual pose of the robot is to equip it with ways to measure its own deformation, for example by placing so-called strain gauges on the surface. Strain gauges are a sensors that measure deformation by way of detecting a change in electrical resistance of a conductor upon deformation. Installing traditional strain gauges on a soft robot has a lot of drawbacks. These sensors are expensive and most often made from metal which would not only hinder the robot in moving but also introduce hard parts to a soft robot. Also, commercial strain gauges are usually designed to measure very small deformations, whereas soft robots often need to deform a lot in order to be useful. However, if the surface of the soft robot were to be made conductive, the robot body itself could be used as a strain gauge. I experimented with different conductive materials in order to come up with a conductive coating. A mixture of carbon black, water, acrylic paint and dish detergent lead to a easy to mix conductive paint. By cutting slits into the foam surface and filling them with the mixture I was able to directly integrate deformation sensors into the robot body.
As a demonstrator for this technique I created a teleoperation setup where a combination of two hand shaped soft bodies are linked together. One hand is strapped to an operators hand and measures the deformation and the other hand will be moved to the same deformation by a set of tendons attached to servo motors. The overall cost to build this setup was less than 100$.
The work I did at the Computational Robotics Lab resulted in a paper with the title Expanding Foam as the Material for Fabrication, Prototyping and Experimental Assessment of Low-Cost Soft Robots With Embedded Sensing. I was invited to present my findings at ICRA2019 in Montreal, Canada.
https://doi.org/10.1109/lra.2019.2893416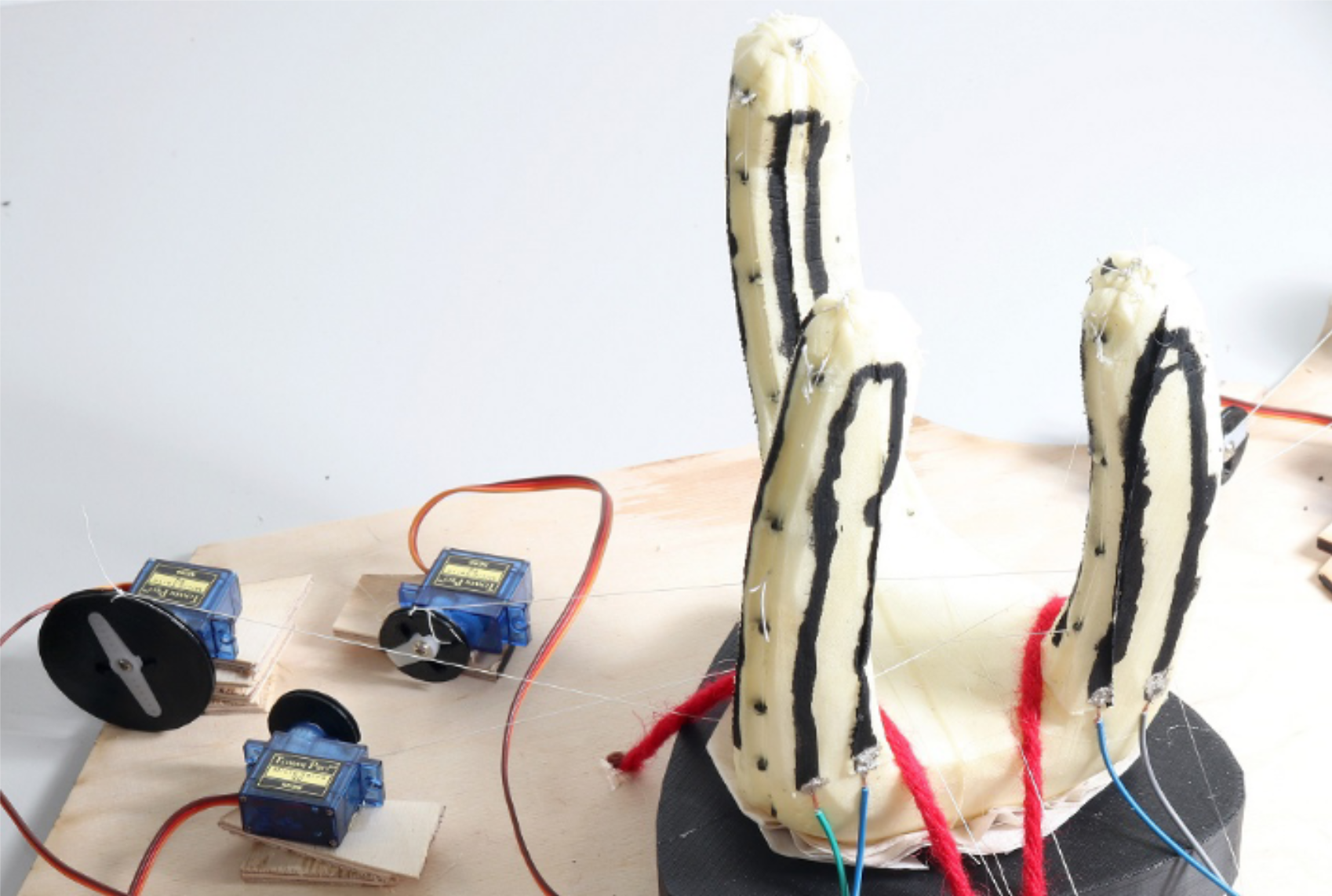